

Job: The material was chilled iron with a hardness of 70 HRC.

Overcoming the Challenges of Threading Hardened Parts Surface finish Ra improved to 20 microinches. Results achieved with the new cutting tool: Cycle time was reduced from 8 minutes, 5 seconds to 1 minute, 23 seconds, and each boring bar now can be used for 75 parts. The inserts have a carbide substrate, a high-temperature-resistant coating and an adapted cutting-edge geometry specifically designed for hard turning materials ranging to 66 HRC. Sales engineer at Horn recommended the Supermini 105 tool system with an HS36-grade boring bar insert. Surface finish obtained is 38-microinch-Ra.

The cycle time for each piece was more than eight minutes. Each corner only lasted for 10 or 15 parts. Problem: The CCMT-type carbide cutting tool insert that the shop was using to bore the hole was causing three specific problems. A 1.5-inch-deep hole is then bored into each piece, holding a tolerance of ☐.0005 inch. The inner and outer diameters are blanked and sent out for case-hardening to 60 HRC. They are made from 1-inch-diameter 8620 alloy steel barstock.
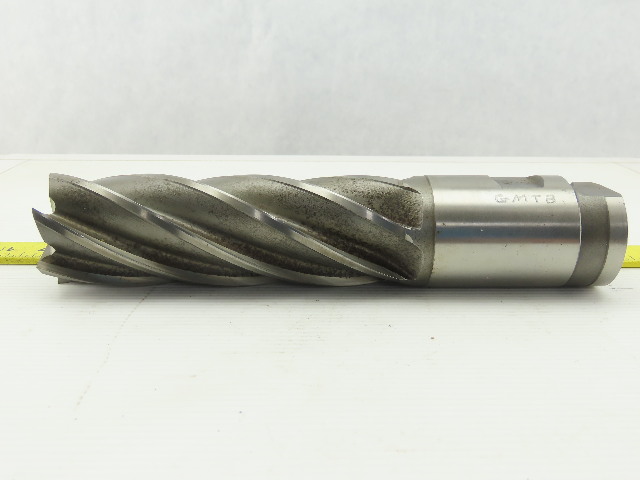
Shop produces 2,000 of these bushings every year. Horn USA’s Supermini type-105 tool system with an HS36-grade boring bar insert reduced this cycle time. Precision Machine’s cycle time to bore a hole in a bushing was more than eight minutes. In the right applications, it can result in cycle time reductions of 50 percent or more.Ĭhanging Cutting Tools Reduces Cycle Time by 7 Minutes in Hard-Turning Application With Sandvik’s new PrimeTurning process, however, you can feed in either direction in turning, facing and shoulder-cutting operations. In conventional turning, you feed toward the chuck in the Z axis. There is a cost advantage also as the CoroDrill DS20 7xD is a latest tool but the cost is equal to that of previous tools.Ĭut Turning Cycle Time by Feeding in Both Directions The drills could drill all 92 holes of the ring without needing to change the inserts (although SKF still changes inserts as a precautionary measure because they operate at higher feed rate). The tests started at feed rates of 114 millimetres per minute, but after making several adjustments, they were able to achieve up to 198 millimetres per minute. In real data, they showed a 100 percent increase in the tool’s service life and a 98 percent increase in productivity, calculated as the ratio between the quantity of material removed and the time taken to produce each part. In 2017 Sandvik Coromant’s drilling experts came up with the solution – the CoroDrill DS20 7xD for the reliability, speed and consistency promised by the new tool.įor the tests carried out on production parts, the cutting conditions were intensified and the diameter was increased to 39 millimetres that gave clear improvements in terms of tool life and a resulting increase in productivity. The uncertainty of tool life resulted in slow drilling feed rates of 102 millimetres per minute and continual halts to prevent damage to the tool, the machine or the workpiece. The parts were produced using special custom-made 6-7xD drills, the tool length made the process more unstable, and production was frequently interrupted by broken inserts. Specialised machining centres are used in which two machines drill holes simultaneously with depths from 39 millimetres to 231 millimetres on a 42CrMo4 ring, up to a total of 92 holes. Job: A wind turbine bearing with a diameter of three metres. Even complex part geometries can be created in a single motion with just one tool. RollFEED® turning: 3-axis turning reduces machining time by up to 80 percentĭramatically shorter cycle times, minimized tool costs, and improved surface quality, even at deeper cutting depths: The advantages of rollFEED® turning from Vandurit are huge. Sandvik GC1525 cermet insert - cost benefit Machine Shop Process Industrial Engineering Įconomic - Cost Analysis - Cutting Tool AlternativesĮconomic analysis of PCD tool in cutting composite materialĬarbon fiber reinforced plastic materials are about 70% lighter than steel and about 40% lighter than aluminum, while costing only about 20% more. These case studies of cutting tool alternatives help industrial engineers in doing machine shop process industrial engineering and machine tool work study.
